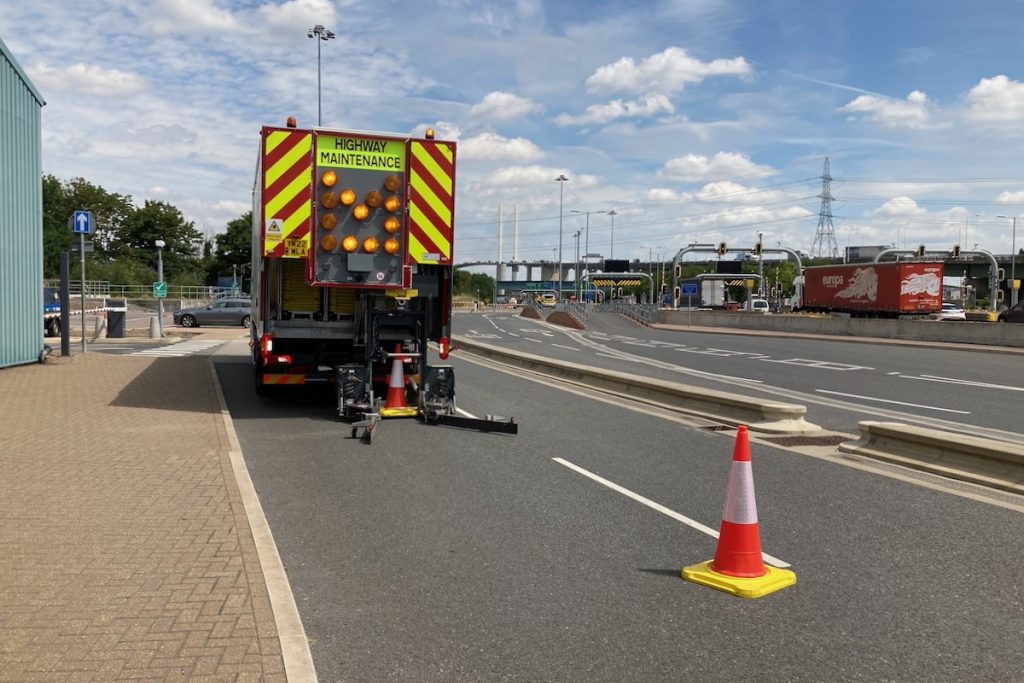
Traffic management operatives on the M25 are set to benefit from reduced risk when implementing lane closures among fast moving traffic following the adoption of automated cone laying machines.
Traditionally, cones are placed on strategic roads manually by an operative standing on the back of a traffic management vehicle. This can put them in harm’s way from a collision or side swipe and operatives have been known to fall onto the carriageway while laying cones. Previous attempts to develop similar cone laying technology are said to have had mixed results.
But now, Balfour Beatty – as part of the Connect Plus Services consortium which manages and operates London’s orbital motorway – is rolling out new ‘Falcon’ machines capable of automating the process.
Developed by manufacturer Highway Care with sponsorship from National Highways, a prototype version of the machine underwent off road testing followed by a year of live trials on various projects across England. National Highways is also supporting the development of a second machine by King Highway Products.
Close to 750km of total lane closure was demonstrated during trials of the prototype Falcon machine. The technology was then subject to a further 12 months of design development – which saw a number of changes made based on operator feedback – and has now received regulatory acceptance.
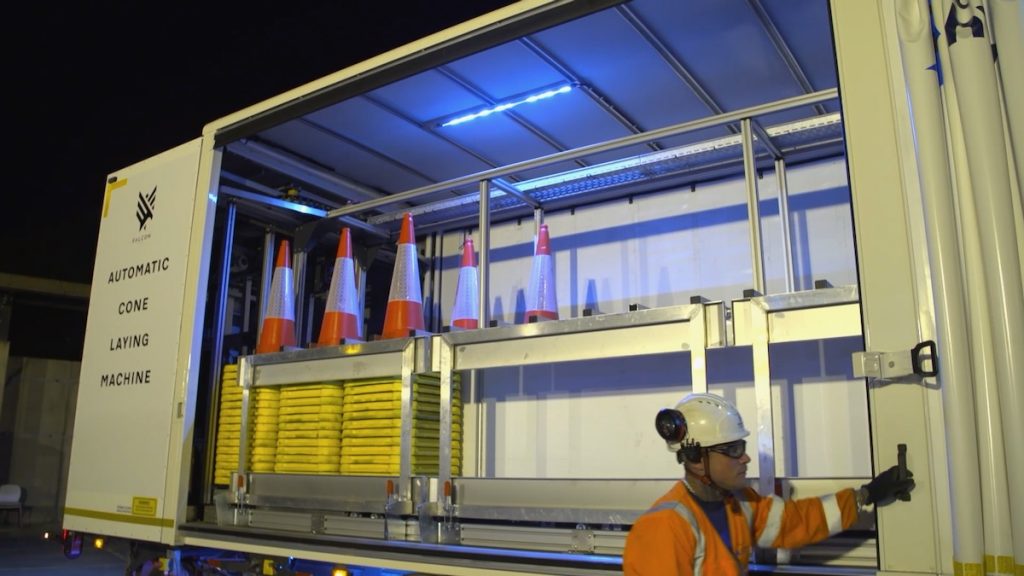
Five of the machines are to be deployed on the M25, the first of which was showcased recently in a launch event at a depot close to the Dartford Crossing.
“I never thought we’d get to this point,” Connect Plus Services’ managing director David Neal told Transport Infrastructure News. “Fifteen years ago I got heavily involved in a prototype vehicle for laying cones, which in short was a total disaster and just didn’t work at all.
“I vowed after that I would never go near another one again. Luckily I changed my mind,” he said, adding that when he heard about the work to develop the Falcon machine he “jumped on board in a flash”.
In a demonstration at the launch event, attendees saw the machine – which is driven by an operative – distribute a line of cones along an empty service road, before reversing back to collect them.
Cones are lowered down by a feeder at the rear of the vehicle and two guiding arms can switch left or right to usher them into the correct position, all while on the move. This allows for a cone taper to be created. The arms form a ‘V’ shape when the vehicle reverses to collect the cones.
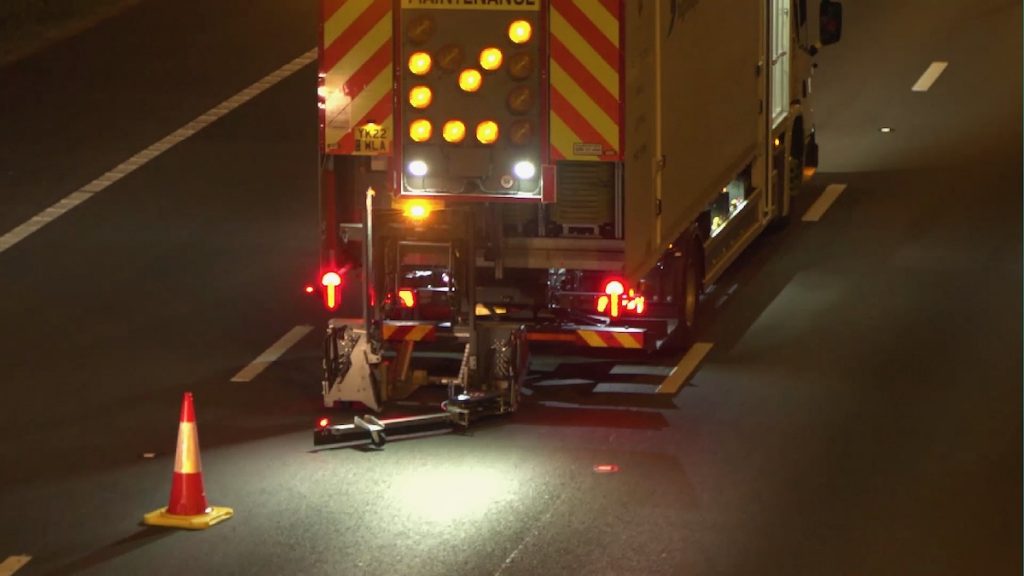
Despite the innovative nature of the technology – which can achieve a minimum spacing between cones of 3m – it is believed to offer little advantage when it comes to productivity. Reducing risk to operatives is the primary driver behind Balfour Beatty’s investment, said the firm’s health and safety director for highways and major projects Steve Crofts.
“The sole focus of this particular piece of kit is health and safety and I think it really demonstrates that we genuinely care about the workforce and that we are truly committed to achieving zero harm.”
He added: “Anyone who has ever introduced anything new anywhere will know it is typically met with cynicism and mistrust. We very quickly got through that to a place where our people are really happy to be using this machine.”
Published on Transport Infrastructure News, July 18 2022